
My father was a journeyman pressman. He owned a small printshop when I was a teenager. At the age of 16, I was going to look for a job. He said “I’ll give you a job in the shop”. I went into the shop after school one day and washed up a printing press for the very first time. It was an AB Dick 360. I applied for and got a job at Wendy’s the very next day. I told my dad that I was NOT going to run a printing press. I thought the whole operation was just disgusting.
Little did I know how much printing I would do in my lifetime. Overall, printing was very good to me.
I started working at Treasure Chest Advertising right out of high school. I had intended to work my way through college but ended up working in printing for decades. Work at Treasure Chest was fast paced and very physical. My first job was to stack grocery store ads on pallets as they came out of the press. That press ran about 60,000 finished newsprint pieces an hour. Many young men were unable to handle the demands of that entry level position. For some, a few hours was enough and turnover was high. However, those that stuck it out were molded into pressmen.
I stayed at Treasure Chest for 5 years, working my way up to 2nd pressman on a heat-set web press. When I walked into that shop, I weighed 110 lbs. 5 years later, I was 160 lbs of solid muscle and a little bit of printing knowledge.
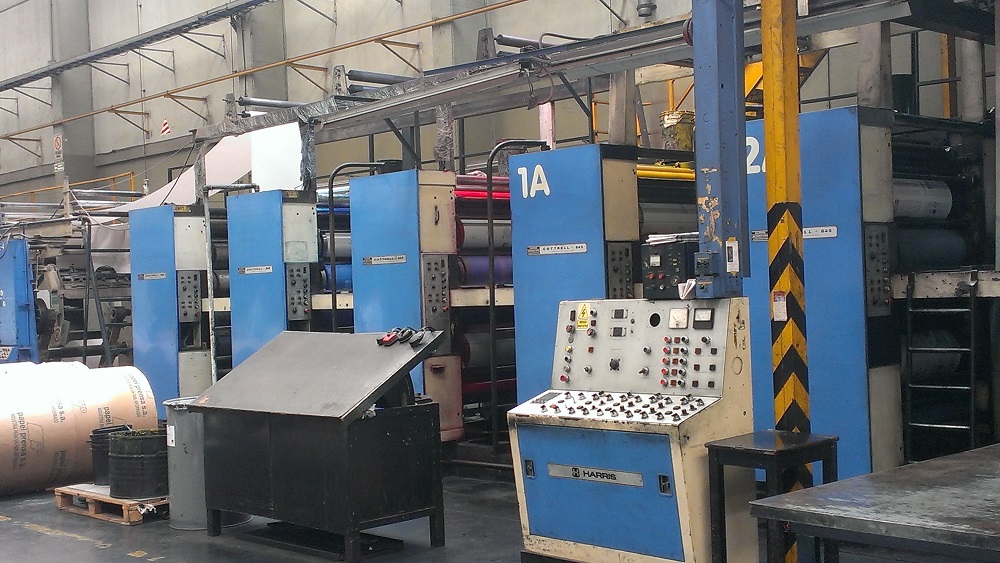
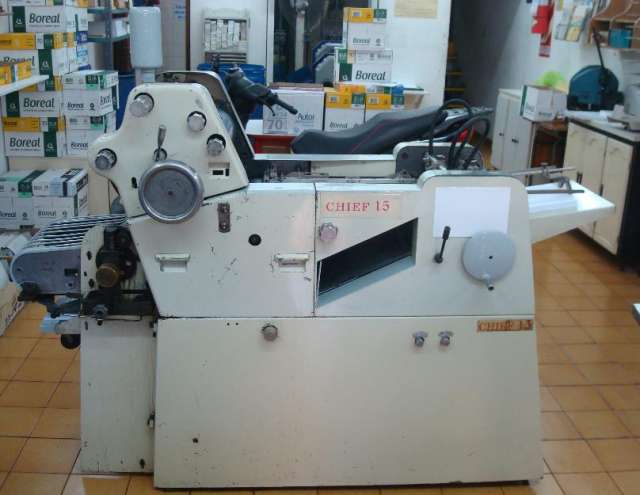
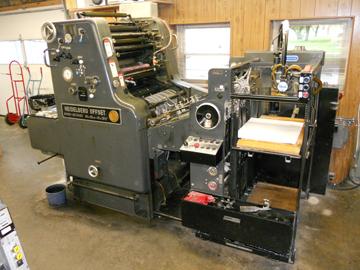
For my next gig, I went from working on the giant web presses to running the smallest sheetfed duplicators. I took a job at Priority Litho running a Chief 15. I spent several years at that shop learning the sheetfed trade. Some really old-school stuff. We shot film on a vertical line camera and stripped it up on a light table. Our plates were hand developed on a sheet of glass. I stayed at Priority Litho long enough to learn to run the single-color Heidelberg SORK. We ran heavy coverage posters for places like Eugene Ballet and Eugene Opera among other things. Ken Kesey was a frequent customer.
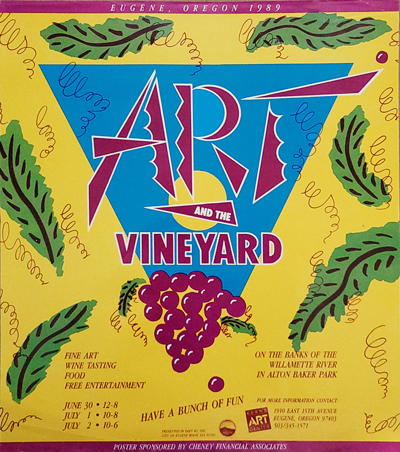
This is also where I really learned about 4 color process printing. Since the Heidelberg was a single color press, we had to do one color at a time. You really have to understand how the colors will interact without watching it in real time.
After lessons learned at Priority Litho, I was drawn to a job at Eugene Print, because I would have an opportunity to run multi-color sheetfed presses. I started there running a Hamada 665 with a common blanket 2nd color head. I also ran a Heidelberg GTO small true two-color press. My ultimate goal there was to run the 5-color Heidelberg MOFP, but that was not meant to be. After I had been there for a few years, Eugene Print purchased a small Didde Apollo web press. Because of the high production I was able to do on that machine, the company felt that it was where they could best utilize my skills.
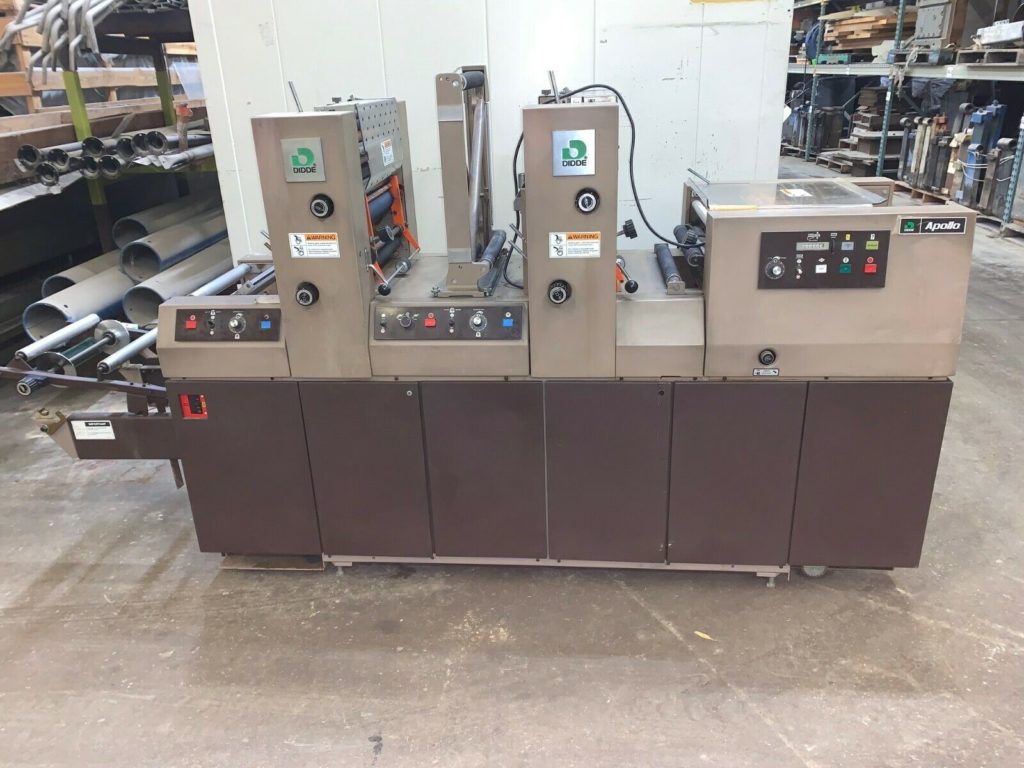
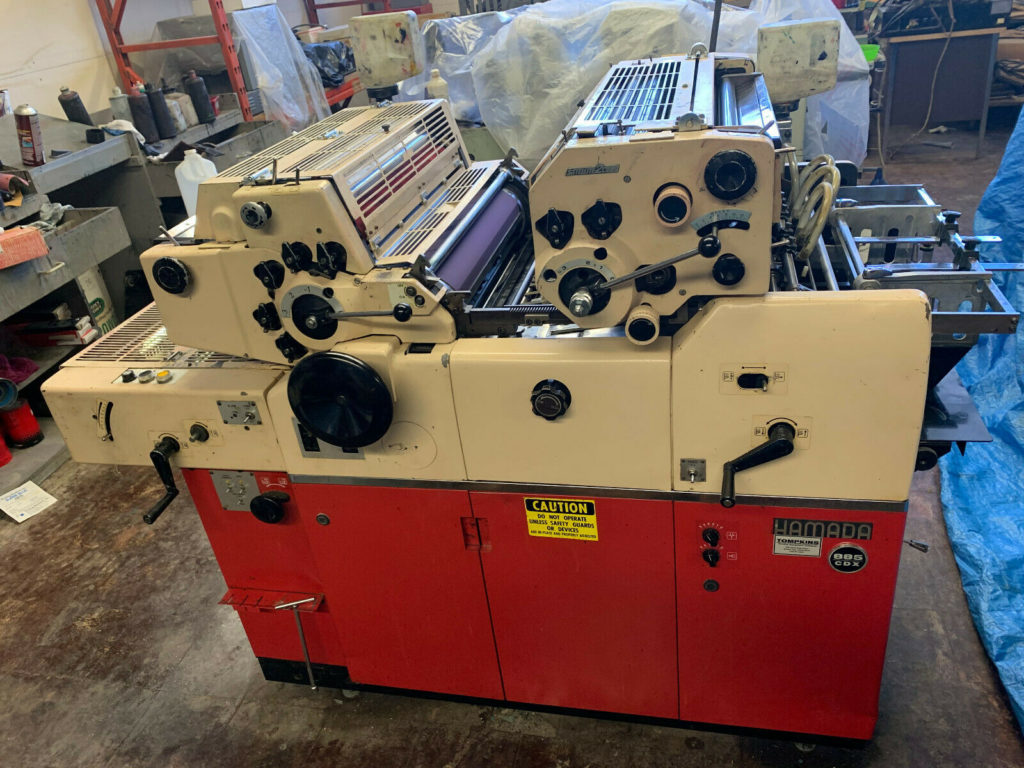
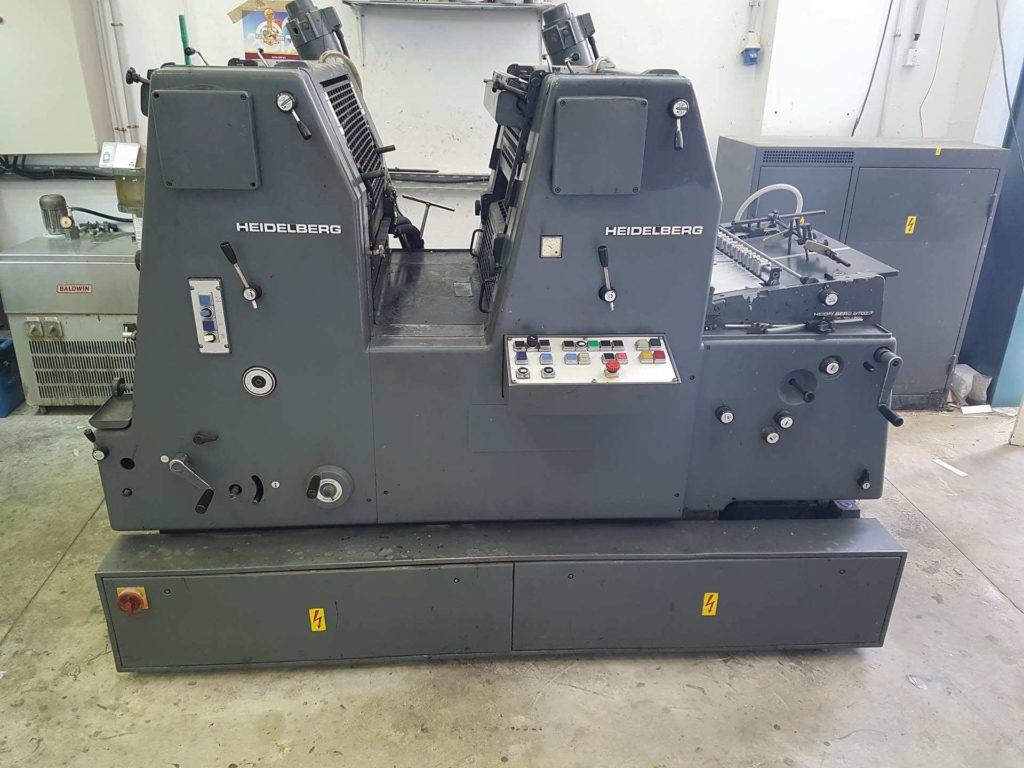
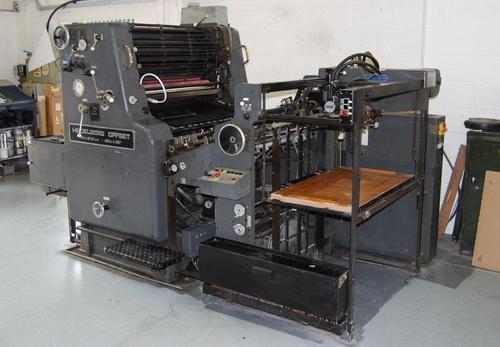
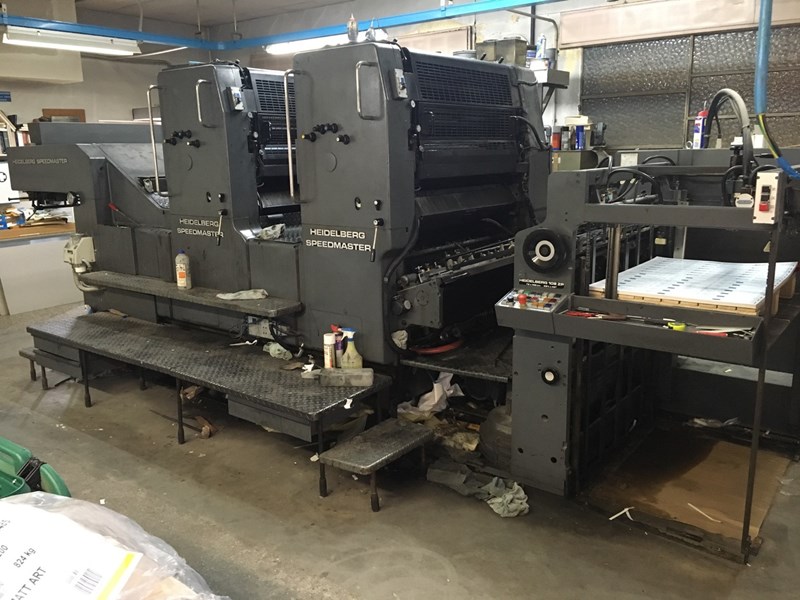
I wanted to run something a little bigger so when a position to run a 40″ press came open at Industrial Publishing, I jumped at the chance. Running sewing patterns on 12 lb bond was an interesting experience. I got advanced lessons in how paper moves through a press from one of the guys there. I was able to do well enough that I earned a promotion to the 40″ two color Heidelberg Speedmaster.
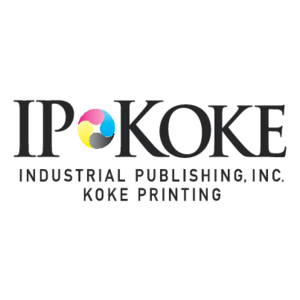
I would have stayed at Industrial Publishing to learn more, but sometimes life changes course.
Life caused me to move to Hemet California without a plan. That was a setback for my printing career. I needed a job quickly and found one at a small printshop running an AB Dick 9810.
I only worked there for about a month before I found a job running another 40″ Heidelberg SORD and a SORZ at Custom Printing in Oxnard California. The Heidelberg SORZ was an interesting configuration. The plate for the first unit was hung from the back of the press while the 2nd unit plate was attached from the front of the press.
Southern California was not a good fit for me. I only stayed at Custom Printing for a few months before I bounced to another job at Ojai Valley News, running a Hamada 612 CD. The management there was really great but still restless, I just couldn’t stay.
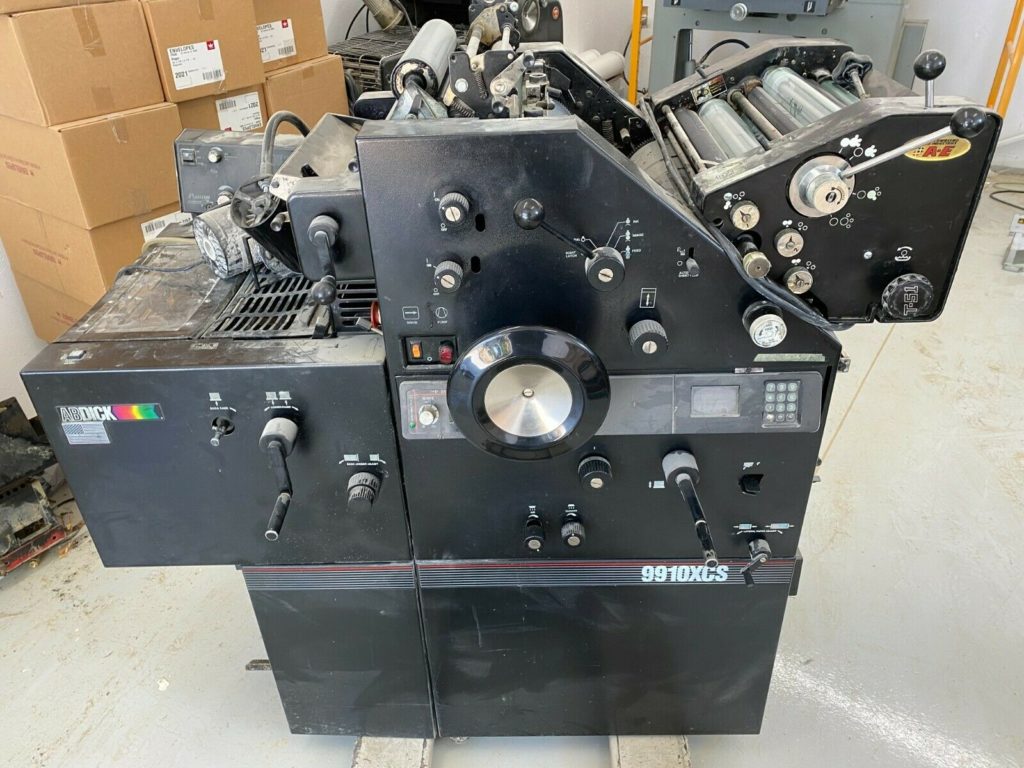
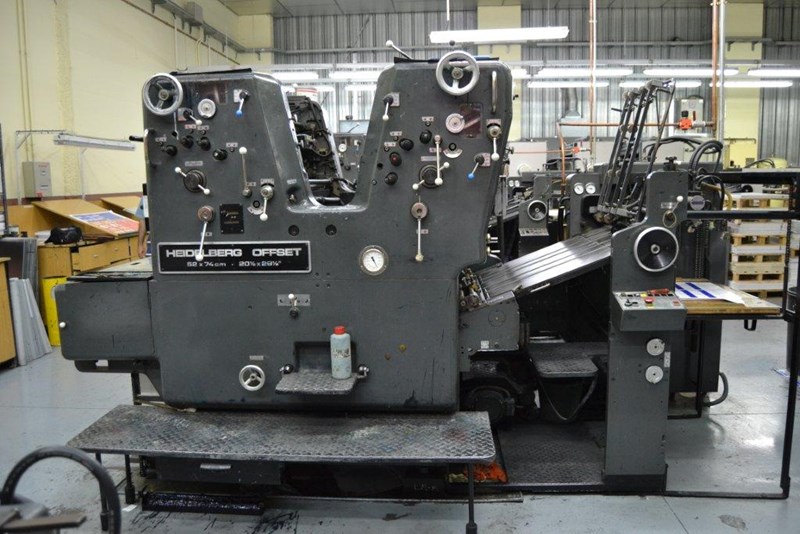
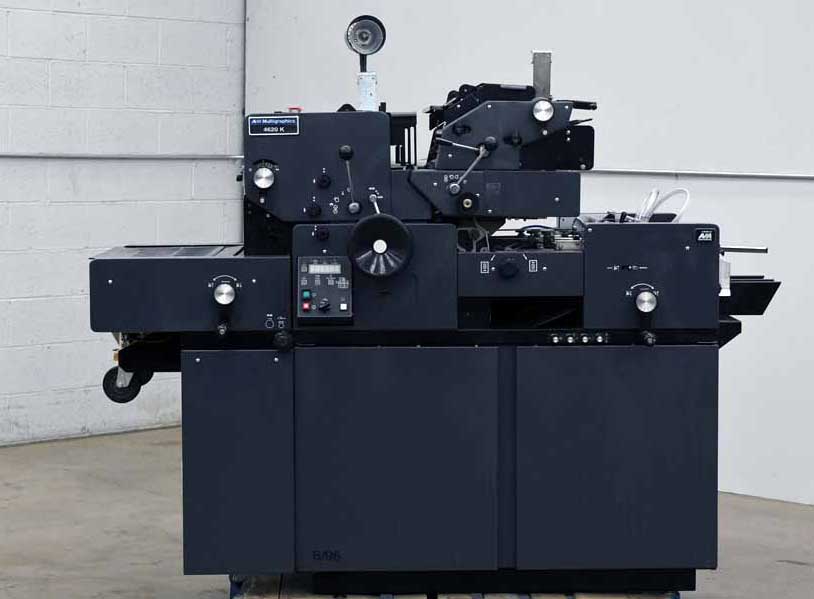
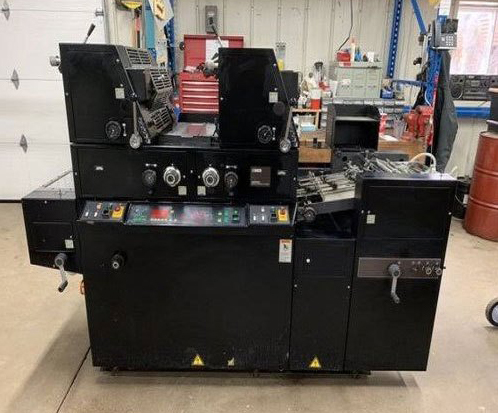
I found a home at Pronto Print in Bend Oregon. I started there running an AB Dick 9810 and an AM Multigraphics 4610. Both of these machines had a common blanket 2nd color head. The Multi had a pull guide and brush wheels for sheet registration. We ran some small 4 color process jobs on that press, but it was inefficient.
Pronto Print upgraded that press to a brand new AB Dick 9985/Ryobi 3302, which is a true 2-color press. We also added an AB Dick DPM2000 digital platemaker.
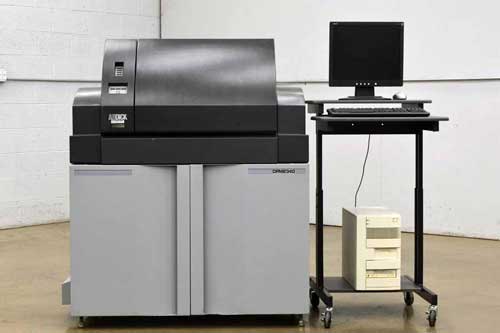
The DPM2000 used a proprietary plate material cartridge that contained the same polyester plate material as other plate cameras but it was much more expensive. I designed a reusable cartridge that could make use of the common rolls of plate material.
While I was at Pronto Print, I took an interest in computers. Jim Sage very generously paid for some computer science college courses and let me serve as the in-house computer technician. I am eternally grateful.
After more than 5 years at Pronto Print, I was ready for a change. I took a job at another shop in Bend at Print Management Group. My job there was to run a Ryobi 3302, but I also had an opportunity to run a 4-color Komori 420. David Sedgwick was a great mentor, teaching me about multi-color press operation.
While at Print Management Group, I served as the in-house computer technician and filled in doing some graphic design and digital prepress work.
I also started “Keith’s PC Service” while at that shop. I left Print Management Group to be my own boss.
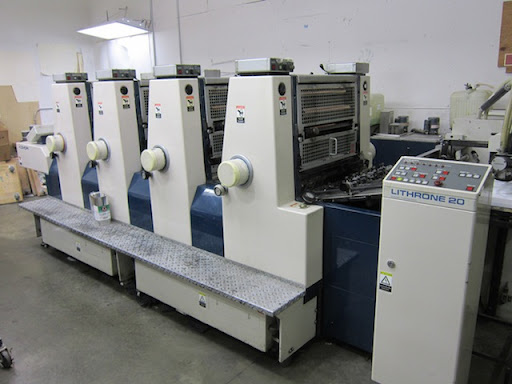
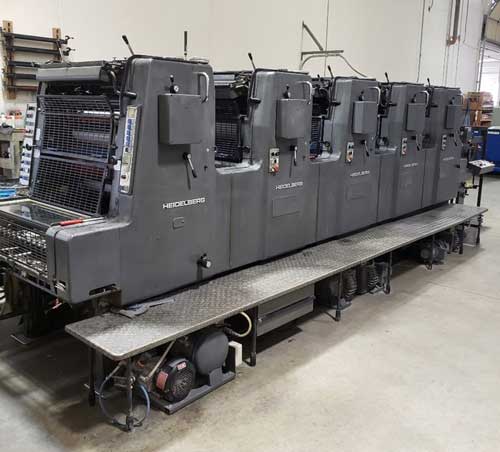
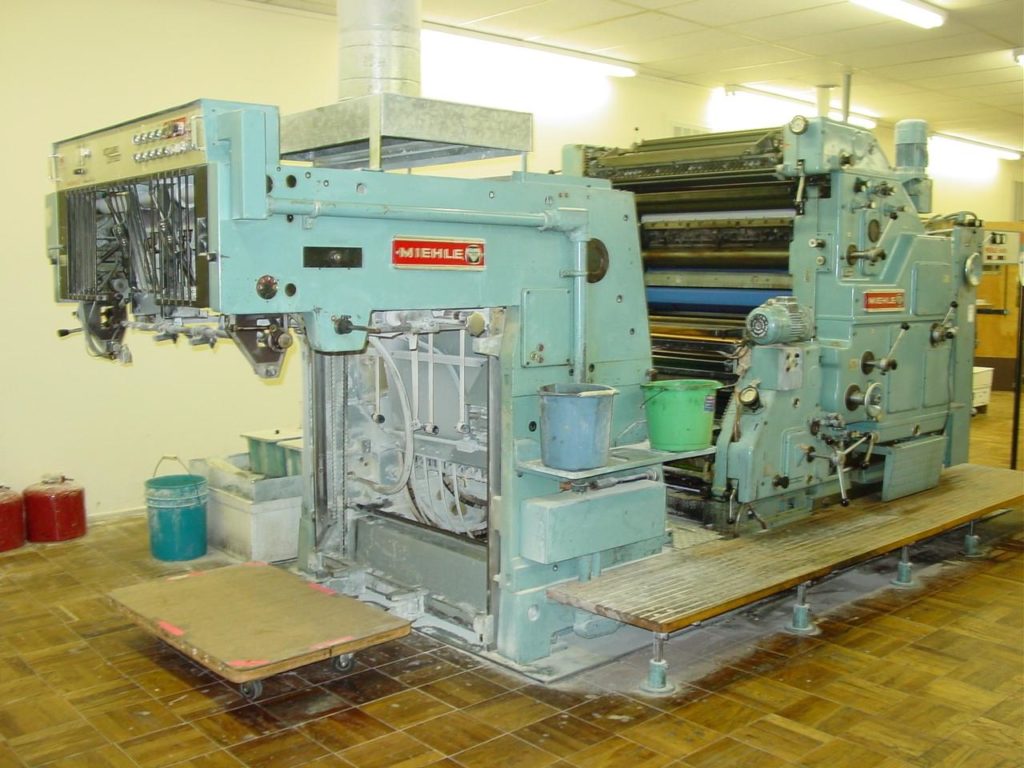
“Keith’s PC Service” didn’t really work out and I once again found myself printing, this time at Graphic Press in Klamath Falls Oregon. I helped to install and then ran a Heidelberg MOFP 5-color press. Graphic Press had a collection of old sheetfed presses and I eventually ran everything in the room. There was a Miehle 38″ 2-color press that we ran furniture box labels on. That thing was a big scary monster. It was built before there were many safety regulations.
The shop was sold and I was promoted to Production Manager. In that capacity, I implemented estimating and job tracking software. I also selected and purchased a digital plate and proofing system. I designed a website to sell ganged 4-color printing online.
In the end, the new owners sold the shop to the competition. I did not stay to work for the new owners.
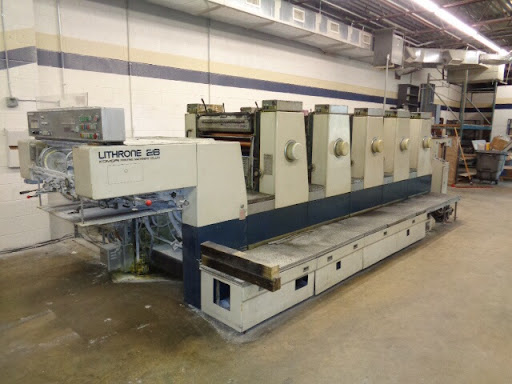
In January of 2007, I started work at Color Magic/Colormation. I stepped away from management and went back to running presses. The shop was a high production 4-color house. We did a lot of gang printing of post cards and brochures. I ran a 5-color Komori L526. We used the 5th unit to apply aqueous coating.
This would prove to be my last full time job in commercial printing. In late 2008 the great recession was starting to take it’s toll. Throughout 2009, the printing industry was shrinking. At the beginning of that year, Colormation had 5 press operators on multiple shifts working overtime. By January of 2010, there were only two of us left. We were each working less than 20 hours a week. I couldn’t find another decent job in printing and made a leap of faith into my career as a computer tech.
My first entry level job as a computer tech did not come close to replacing my printing income. I was forced to take a second job. I thought I would have to moonlight for 6 months or maybe a year. I ended up working my weekends at JB Printing and Graphics for about 7 years.
If you had to work a second job, you couldn’t find better people to work for than Jody and Dennis Burnim. I started that job out of necessity, but they treated me like family. I am forever grateful that I found these lifelong friends.
This is a video of the very last time I inked up a press. When I got ready to leave that job, my wife insisted that she needed a lifetime supply of personalized notepads. That’s what’s running in the video.